製造業の「ポカミス」対策~根本原因と防止策徹底解説~
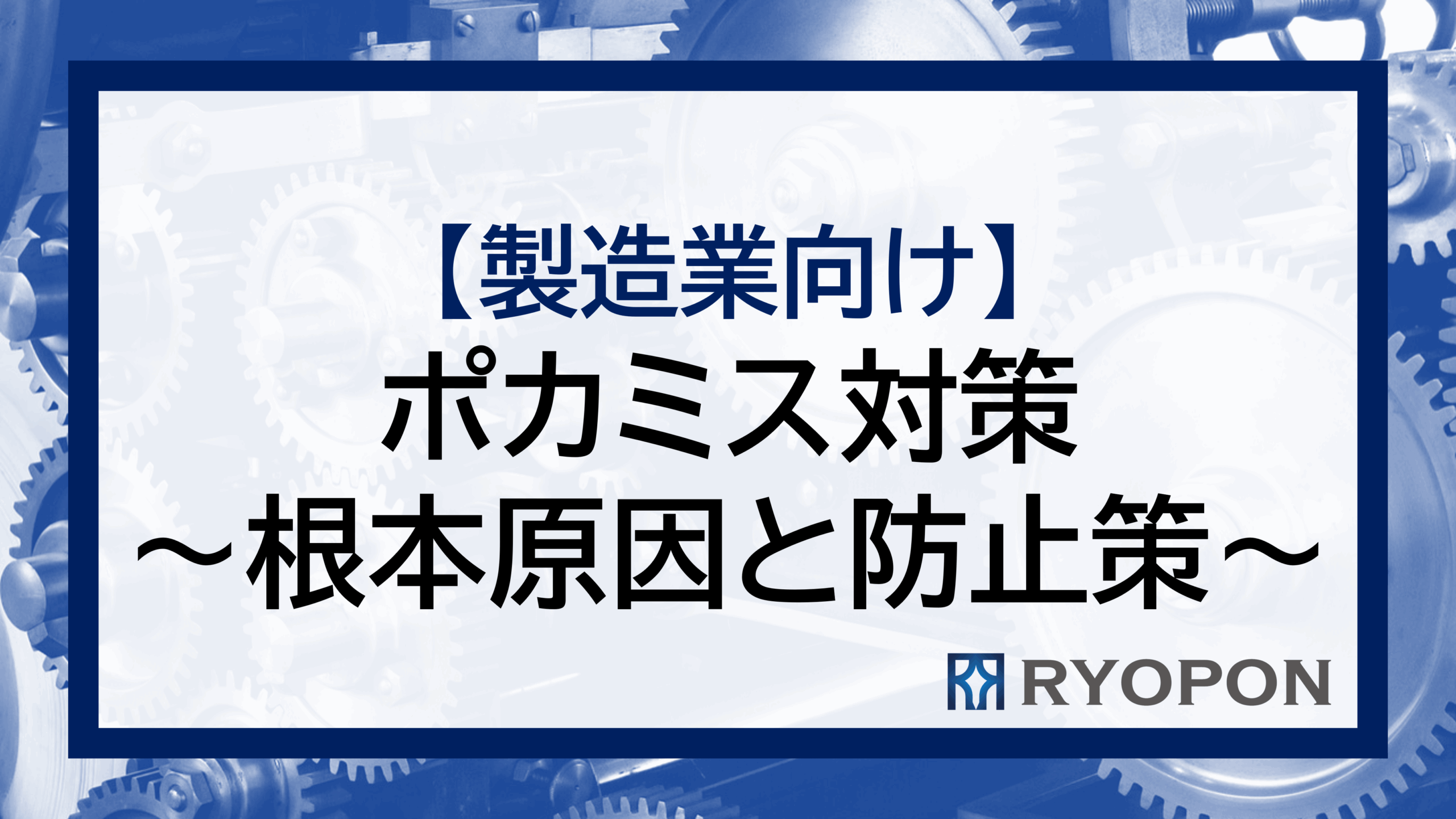
製造業収益改善パートナーの北澤です。皆さんの工場では、「ポカミス」が原因で頭を悩ませてはいませんか?ポカミス、つまり作業者の方の不注意や思い込みから生じる「うっかりミス」は、一つひとつは小さくても、積み重なると生産効率や品質に深刻な影響を及ぼし、コストの増加や納期の遅延といった経営課題に直結してしまう、非常に厄介な問題です。
しかし、諦める必要はありません。なぜミスが起きるのか、その根本原因をしっかりと突き止め、一つひとつ対策を講じていくことが何よりも重要です。例えば、作業手順の見直しや、より実践的な教育・訓練の強化。あるいは、現場の環境整備やツールの改善も非常に有効な一手となります。
ポカミスとは、そもそも何なのか?
改めてご説明しますと、ポカミスとは製造現場などで作業者の方が不注意や誤操作によって引き起こしてしまうミスの総称です。これが侮れないのは、たとえ小さなミスであっても、生産ライン全体や製品の品質に大きな影響を与えてしまう点にあります。
具体的な例を挙げれば、部品の取り間違い、作業手順の飛ばし、検査の見逃しといったところでしょうか。こうしたポカミスが連鎖的に発生すると、製品不良や納期遅延といった、お客様からの信頼を損なう事態を招きかねません。
ポカミスを「仕方ないもの」として放置することは、企業の信頼性を揺るがし、最終的には収益に直接的なダメージを与えます。だからこそ、根本的な原因をしっかりと把握し、的確な対策を打つことが、今まさに求められているのです。
なぜ製造現場でポカミスは発生するのか?
製造業におけるポカミスは、本当に様々な要因が絡み合って発生します。まず一つ目に考えられるのが、作業環境の整備不足です。工具や部品が整理されていなかったり、騒音がひどかったりする現場では、作業者の方の集中力がどうしても削がれてしまい、ミスが発生しやすくなります。
次に、人材の教育・訓練不足も大きな要因ですね。特に新人の方や、まだ技能が未熟なスタッフの方は、作業手順を誤って覚えてしまうことがあります。ここは丁寧に、根気強く指導していく必要があります。
さらに、作業手順そのものが不明確であるケースも少なくありません。誰が見ても同じように作業できる標準作業手順書がなければ、現場での判断が個人に委ねられ、ミスが頻発する原因となってしまいます。
これらの根本原因を一つひとつ解き明かし、適切な対策を講じることが、ポカミスを減らすための確実な第一歩と言えるでしょう。
ヒューマンエラーがもたらす影響
人が作業を行う以上、「ヒューマンエラー」を完全になくすことは難しいかもしれません。しかし、作業者の注意力が散漫になったり、知識や技術が不足していたりすると、設計ミスや生産ミスにつながる可能性は格段に高まります。その結果、製品の品質が低下し、大切なお客様からの信頼を失ってしまうことにもなりかねません。
また、ヒューマンエラーはコストの増加という直接的な打撃ももたらします。ミスを修正するための手戻り作業や、最悪の場合は製品の再製造が必要になれば、人件費や材料費など、多くの資源が無駄になってしまいます。特に、限られたリソースで運営されている中小企業にとって、この影響は非常に大きいものがあります。
こうしたリスクを減らすためには、作業環境の整備や、現場に即した正確な教育訓練が欠かせません。ミスを減らし、より効率的な生産体制を構築していくことこそが、これからの製造業の進化につながるのです。
作業環境や設備の問題を見過ごさない
製造業のポカミスを考える上で、意外と見落とされがちなのが作業環境や設備の問題です。例えば、作業場が整理整頓されていないと、必要な工具や部品を探すのに時間がかかり、作業の流れが止まってしまいます。この「探す」という無駄な時間が、焦りを生み、ミスを誘発するのです。
また、工場の照明が暗かったり、騒音が大きかったりするのも問題です。視認性が低ければ部品の誤認や操作ミスにつながりますし、騒音がひどい環境では、作業指示が正確に伝わらず、コミュニケーションエラーから誤解が生まれることもあります。
さらに、設備の老朽化やメンテナンス不足も深刻です。機械の動作が不安定だと、作業者の方はいつも以上に気を張る必要があり、精神的な負担から冷静な判断が難しくなり、結果としてポカミスが発生しやすくなるというわけです。
「手順の不明確さ」がミスを招く
ポカミスの温床となりやすいのが、手順の不明確さです。標準作業手順が不十分だったり、内容が現場の実態と合っていなかったりすると、作業者の方は「どう進めるのが正しいのか?」と混乱してしまいます。特に、複数の工程が複雑に絡み合う作業では、正確な手順書がなければミスのリスクは飛躍的に高まります。
また、手順書があったとしても、その内容が現場の作業者の方にきちんと理解されていなければ意味がありません。自己流の判断で作業が進められることが多くなり、それが誤った判断や作業の遅延を引き起こし、製品の品質低下や納期遅延につながってしまうのです。
こうしたリスクを避けるためには、誰が見ても分かりやすく、具体的な作業手順の策定が不可欠です。定期的に手順を見直し、現場の意見を積極的に取り入れることで、ポカミスを防ぎ、効率的な製造プロセスを実現することができます。
ポカミスを防ぐための具体的な対策
では、どうすればポカミスを防げるのか。ここでは効果的な対策をいくつかご紹介します。まず第一に、作業手順の明確化です。誰が見ても一目で理解できるような、写真やイラストを多用した手順書やチェックリストを用意することで、作業者の方が迷うことなく業務を進められるようになります。
次に、定期的な教育訓練の実施です。これは非常に重要ですね。新しく入ったスタッフの方はもちろん、業務内容が変更になった際にも、徹底した研修を行い、必要な技術や知識をしっかりと身につけてもらうことが求められます。
さらに、現場環境の整備も忘れてはなりません。作業スペースを整理整頓し(5S活動ですね)、必要な道具や資材が「いつも」「決まった場所に」ある状態を作ることで、作業者のストレスを減らし、集中力を高めることができます。こうした地道な対策の積み重ねが、ポカミスのリスクを大幅に軽減してくれるのです。
原因分析の重要性
ポカミス対策で最も重要なのは、発生したミスの根本原因を徹底的に分析することです。多くの企業では、ミスが起こるたびに対処療法的な対策を講じがちですが、これでは同じようなミスが何度も再発してしまいます。
「なぜなぜ分析」などの手法を用いて原因分析を行うことで、「なぜそのミスが起きたのか」という具体的な問題点を可視化できます。作業手順に問題があったのか、それとも環境に要因があったのか。現場の作業者の方々と対話を通じて真の原因を洗い出すことが、効果的な対策の出発点となります。
また、原因を特定することで、対策を講じた後の効果測定がしやすくなるというメリットもあります。改善が進んでいるかどうかをデータで評価し、次のPDCAサイクル(計画・実行・評価・改善)を回していくことが可能になるのです。
作業ルールの見直し
作業ルールの見直しは、ポカミスを防ぐための基本中の基本です。現場の状況や扱う製品は日々変化するのですから、ルールも一度作って終わりではなく、定期的に見直す必要があります。
まずは、現在の作業手順を現場で詳細に確認し、問題点や非効率な部分を洗い出しましょう。この時、実際に作業している方からのフィードバック(意見)を聞くことが何より重要です。教科書通りのルールではなく、現場の実態に合ったルールでなければ意味がありませんからね。
そして、洗い出した課題をもとに、明確でシンプルな作業ルールを再構築します。誰でも簡単に理解できるよう、手順書やマニュアルを改訂し、周知徹底することが重要です。このように、作業ルールを現場と共に「育てていく」という意識が、ポカミスの発生を未然に防ぐのです。
作業員の教育と指導
作業員の方々への教育と指導は、ポカミス対策の根幹をなす要素です。特に製造業の現場は、作業が複雑化しがちで、新人や未経験者の方がミスをしやすい環境にあります。だからこそ、効果的な教育プログラムを構築し、継続していくことが求められます。
効果的なのは、OJT(On-the-Job Training)などの実践的なトレーニングです。ただマニュアルを読ませるだけでなく、実際の作業を通じて業務の流れを身体で覚えてもらうことで、理解度は格段に深まります。
加えて、定期的なフィードバックも非常に大切です。作業後に1対1で振り返りの時間を設け、良かった点や改善すべき点を具体的に伝えることで、作業員の方のモチベーションを高め、次なる成長へとつなげることができます。丁寧な教育と指導こそが、品質向上の揺るぎない土台となるのです。
設備投資による改善
時には、設備投資によってポカミス問題を劇的に改善することも可能です。先進的な設備や自動化システムを導入することで、人が介在することによるミス、つまりヒューマンエラーを物理的に減らすことができます。例えば、単純な繰り返し作業や、精度が求められる検査工程にロボットや自動機を導入すれば、作業者の負担を軽減し、ミスの発生そのものを防ぐことができます。
また、最新の設備を導入することで作業環境が整備され、結果として作業者の集中力が向上するという効果も期待できます。見やすい表示器や、直感的に操作できるパネルなども、作業時の誤認や誤操作を防ぐのに役立ちます。
もちろん、設備を導入した後のメンテナンス体制の強化も重要です。これにより、予期せぬ故障によるダウンタイムを減らし、生産性を高めることができます。設備投資は、ポカミス抑制と業務効率向上の両方を実現する、強力な一手となり得ます。
システム導入による対策
システム導入も、ポカミス対策において非常に効果的なアプローチです。特に、手作業での管理や記録に起因するミスを防ぐために、生産管理システムや監視システムを導入することが推奨されます。
例えば、生産管理システムを導入すれば、製品の進捗や部材の在庫状況をリアルタイムで正確に把握できます。これにより、勘や経験に頼った管理から脱却し、誤発注や納期遅延といったリスクを大幅に軽減できます。
さらに、近年注目されているIoT技術を活用したモニタリングシステムも有効です。機械の稼働状況や作業環境の温度・湿度などを常に監視し、異常を早期に検知することで、大きなトラブルにつながる前に対処できるようになります。システムという「賢い仕組み」を導入することで、より効率的で安全な製造現場を実現できるのです。
継続的なチェックと改善
ポカミス対策は、一度行ったら終わり、というものではありません。効果を持続させるためには、定期的なチェックと改善が不可欠です。構築した作業プロセスや品質管理の仕組みが、今も正しく機能しているか、形骸化していないかを定期的に見直すことで、潜在的な問題点を早期に発見できます。
その際、現場の作業者の方々からのフィードバックを積極的に収集することが重要です。実際に作業しているからこそ気づく問題点や改善のヒントは、宝の山です。
そして、改善策を実施した後は、必ずその効果をデータに基づいて定量的に評価しましょう。「ポカミスが何件から何件に減った」というように、数値で効果を把握することで、何が有効で、次に何をすべきかが明確になります。この地道なプロセスを回し続けることで、持続的な改善が実現し、ポカミスが起こりにくい強い現場が作られていくのです。
ポカミス対策の具体的な事例紹介
ここでは、私たちが実際に支援してきた製造現場でのポカミス対策事例を、少しだけご紹介します。
一つ目は、作業手順の「見える化」です。ある企業では、ベテラン社員の頭の中にしかない複雑な手順が多く、若手がミスを繰り返していました。そこで、作業フローを写真やイラストで分かりやすくまとめ、作業場の各所に掲示しました。これにより、誰でも正しい手順を手軽に確認できるようになり、ポカミスの発生率が劇的に減少しました。
次に、ダブルチェック制度の導入です。特にミスが許されない重要な工程において、作業者と確認者を明確に分け、お互いにチェックし合う仕組みを取り入れました。これにより、一人目の見逃しを二人目が防ぐという安全網が機能し、ミスの流出を未然に防ぐことに成功しました。
こうした具体的な対策にご関心がある方は、ぜひ一度、当社の無料相談をご活用いただければと思います。
ヒューマンエラーの防止事例
ヒューマンエラーを防ぐための、さらに具体的な事例をご紹介しましょう。
ある工場では、まず作業環境の徹底的な整備から着手しました。工具や部品の配置ルール(定置化)を定め、誰が使っても同じ場所に戻すことを徹底しました。この結果、モノを探す時間がゼロになり、作業者は本来の業務に集中できるようになりました。
次に、作業手順書の見直しです。文字ばかりで分かりにくかった手順書を、イラストや写真をふんだんに使って、視覚的に理解しやすいように作り変えました。特に注意すべきポイントは赤字で強調するなど、一目で分かる工夫を凝らし、ミスの減少に成功しました。
さらに、定期的な教育・訓練の実施も欠かせません。新人教育はもちろん、経験豊富なベテラン社員にも定期的に再教育の機会を設けることで、ルールの形骸化を防ぎ、現場全体の意識向上を図りました。これらの地道な取り組みが、ヒューマンエラーを効果的に抑制するのです。
作業環境の改善事例
作業環境の改善は、ポカミス対策の非常に重要な柱です。ある製造業の企業では、作業台や棚の配置を根本から見直しました。
まず、作業者の身長や利き手に合わせて作業台の高さや場所を調整し、身体への負担と無駄な動きを徹底的に減らしました。また、「5S(整理・整頓・清掃・清潔・躾)」に基づき、部品や工具を常に決まった位置に置くことを徹底しました。これにより、必要なものを探すことなく、すぐに手に取れるようになり、作業効率が飛躍的に向上しました。
さらに、作業スペースを十分に確保し、通路を広げることで、人とモノの接触による事故のリスクも低減させました。その結果、ポカミスが劇的に減少しただけでなく、作業者の方々のストレスも軽減されるという、素晴らしい好循環が生まれました。作業環境の改善は、全ての製造業の皆様が参考にできる、効果の高い取り組みと言えるでしょう。
設備導入による成功事例
製造業のポカミス対策として、設備導入がいかに効果的かを示す成功事例をご紹介します。
ある中小企業では、これまで人の目に頼って行っていた部品の検査業務で、見逃しや誤検査が多発していました。そこで、最新の画像検査装置を導入し、検査工程を自動化しました。
この新しい設備は、人間では見分けがたい微細な欠陥も高精度で検出できるため、誰が作業しても常に一定の高い品質を保つことが可能になりました。また、検査時間が大幅に短縮されたことで、従業員の方は検査結果の分析や改善活動といった、より付加価値の高い業務に集中できるようになったのです。
この取り組みにより、ポカミスはほぼゼロになり、製品の品質向上と生産性向上を同時に実現することに成功しました。設備投資は初期コストこそかかりますが、長期的な視点で見れば、それを上回る大きなリターンが期待できる好例です。
ポカミス対策に本当に必要なこと
さて、ここまで色々な角度からお話ししてきましたが、ポカミス対策を進める上で本当に必要なポイントを整理してみましょう。
まず第一に、作業環境の整備です。整理整頓された安全な作業場は、作業者の方の集中力を高め、ミスが起こりにくい土壌を作ります。
次に、現場に即した適切な教育・訓練です。作業者全員が正しい手順を理解し、高い意識を持って作業に臨むことが、ポカミスを減らすための鍵となります。
さらに、作業手順の標準化も極めて有効です。誰が見ても分かりやすく、迷わず作業できる手順書があれば、個人の判断によるバラツキやミスを防ぎやすくなります。これらの基本的な対策を愚直に実行することが、強い現場を作るのです。
リスクアセスメントの実施
リスクアセスメント、つまり「危険性の事前評価」は、ポカミス対策の重要な一環です。製造現場にどのようなリスクが潜んでいるかを事前に特定し、その影響度を評価することで、優先順位をつけて具体的な対策を講じることができます。
まずは、作業手順や環境に潜む「ヒヤリハット」の事例などを集め、リスクを洗い出しましょう。次に、それぞれのリスクが「どのくらいの頻度で起こりそうか」「起きたらどれくらい影響が大きいか」を評価します。このプロセスを通じて、どこに重点的に対策を打つべきかが明確になります。
そして最後に、特定したリスクに対する具体的な対策を計画し、実行に移します。このリスクアセスメントを定期的に行い、内容を見直していくことで、現場の安全性と効率性をさらに高いレベルへと引き上げることが可能になります。
定期的な作業手順の確認
定期的な作業手順の確認は、ポカミスを防ぐ上で地味ながら非常に重要な活動です。企業の成長や技術の進化に伴い、最適な作業手順は変化していくものです。そのため、定期的に手順書を見直し、現状に最も適したやり方を維持することが求められます。
この手順の確認プロセスは、作業者の方々のスキルアップの絶好の機会にもなります。新しく導入された設備の使い方や、変更された手順について皆で確認することで、知識の共有が進み、チーム全体のレベルアップにつながります。
その際、確認した内容を議事録として記録し、手順書を更新していくことで、改善活動が形として残ります。こうした地道な取り組みの積み重ねが、ポカミスを防ぎ、製造現場の生産性向上に大きく寄与するのです。
フールプルーフ設計の考え方
フールプルーフという言葉をご存知でしょうか。これは、ポカミスを未然に防ぐための、非常に賢い設計思想です。簡単に言えば、「人間は間違いを犯すもの」という前提に立ち、間違った操作をしようとしても、物理的にできないようにする、あるいはミスに気づかせる仕組みのことです。
例えば、部品の向きを間違えたら、そもそも組み立てられないような形状にしたり、正しい手順で操作しないと次のステップに進めないようなインターフェースを設計したりすることです。また、異常があれば警告音やランプで知らせる、といったこともフールプルーフの一環です。
このようなフールプルーフの考え方を設備や治具に導入することで、作業者の注意力だけに頼ることなく、仕組みでポカミスを大幅に減少させることが可能になります。利益改善を目指す上で、非常に強力な武器になると言えるでしょう。
継続的な教育とトレーニング
ポカミス対策を考える上で、継続的な教育とトレーニングは、絶対に欠かすことのできない車の両輪です。製造現場は常に変化しており、新しい技術や改善手法が導入されれば、当然、作業内容も変わっていきます。
定期的な研修やトレーニングを実施することで、作業者の方は常に最新の知識やスキルを維持し、自信を持って作業に臨むことができます。また、過去の失敗事例や成功事例を全社で共有する場を設けることで、組織全体で学び合い、成長していく文化を醸成することが重要です。
このように、教育とトレーニングを一度きりで終わらせず、継続的に行うことによって、ポカミスを未然に防ぐ強固な体制を築くことができます。効果的な教育制度を整えることは、組織全体の生産性向上に直結する、未来への投資なのです。
まとめ:ポカミス対策は、企業の未来をつくる投資です
ここまでお話ししてきたように、製造業においてポカミスを防ぐための対策は、避けては通れない非常に重要なテーマです。ポカミスが発生すると、品質の低下やコストの増加だけでなく、社員のモチベーション低下やお客様からの信頼失墜にもつながりかねません。
まずは、皆さんの現場の作業フローを見直し、誰でも同じ品質で作業できる「標準」を作ることから始めましょう。そして、定期的な教育・訓練を通じて作業者の方々の意識とスキルを高め、ミスを誘発するような環境要因を一つひとつ改善していくことが大切です。
最後に、ポカミス対策は単なる事故防止活動ではありません。安全で効率的な製造現場を実現することは、企業の競争力を高め、未来の利益を生み出すための重要な投資です。もし皆さんの現場でポカミスにお悩みでしたら、一人で抱え込まずに、ぜひ一度、私たちのような専門家にご相談ください。きっと、お力になれることがあるはずです。