工場の「あるある」を解決!現場で本当に役立つマニュアル作成の秘訣
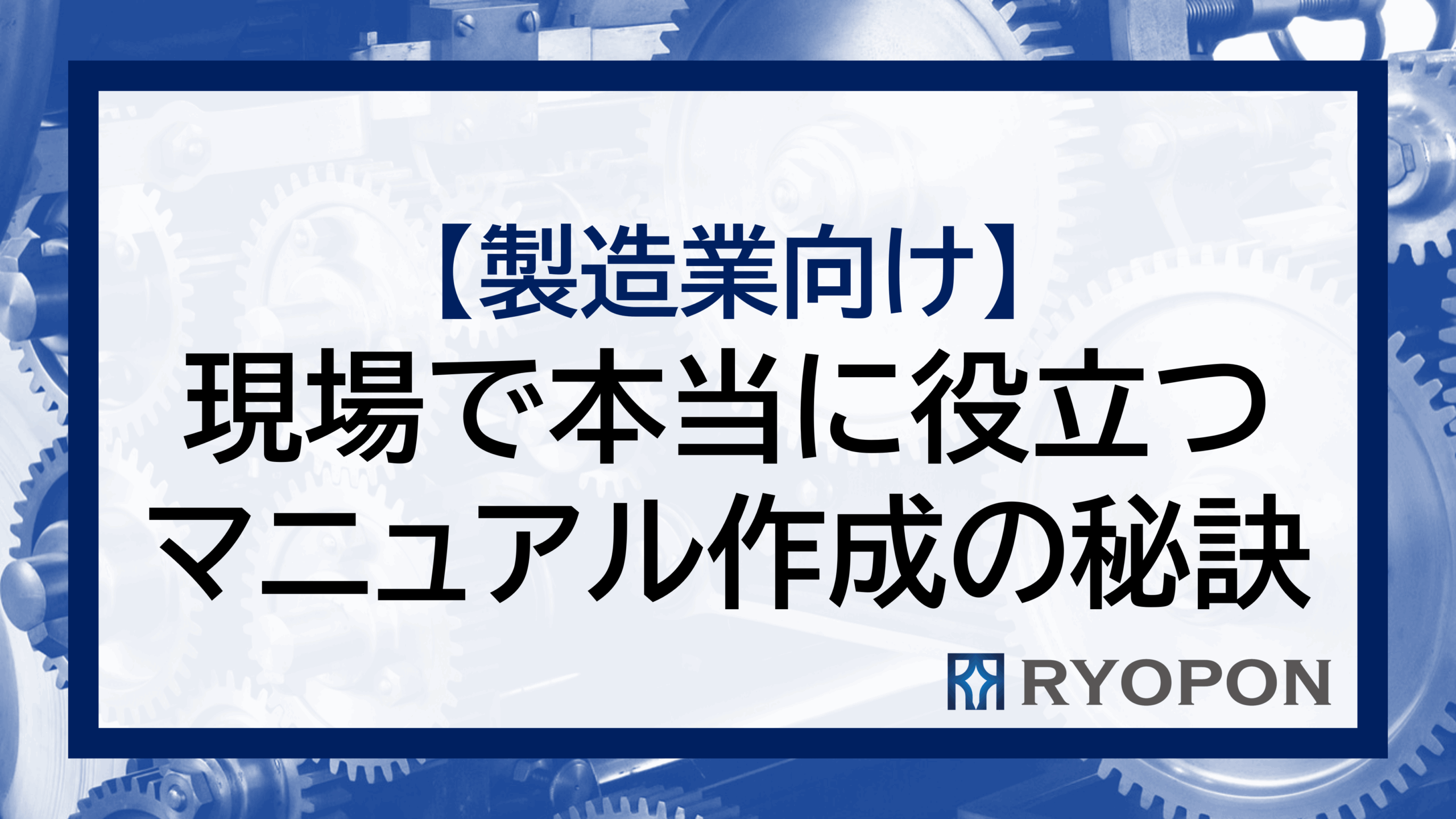
1. はじめに:工場のマニュアル、ちゃんと使われていますか?
こんにちは!製造業収益改善パートナーの北澤です。日々の生産、本当にお疲れ様です。
ところで、皆さんの工場にはたくさんの「マニュアル」があると思います。
機械の操作、作業の手順、安全ルール…
でも、正直なところ、「作ったはいいけど、棚の奥でホコリをかぶってる…」なんてこと、ありませんか?
「あの作業、人によってやり方が微妙に違うんだよなぁ」とか、「新人に教えるのが毎回大変で…」なんて悩み、よく聞きます。
実は、その「使われないマニュアル」こそが、品質のバラつきや、なかなか減らないムダ、ヒヤリとする瞬間の原因になっているかもしれないんです。
でも、大丈夫です!
もしマニュアルが「現場で本当に役立つ」ものになったら、これらの問題は大きく改善できます。
この記事では、その秘訣を皆さんと一緒に考えていきたいと思います。
「使えるマニュアル」を作るための具体的なコツ、そして、なぜそれが重要なのかを、分かりやすくお伝えしていきますね。
2. なぜ?製造現場で「使えるマニュアル」が絶対に必要な3つの理由
「マニュアルなんて、なくても現場は回るよ」そう思う方もいるかもしれません。
ですが、本当にそうでしょうか?実は、「使えるマニュアル」には、皆さんの仕事を楽にし、会社全体の力を強くする、すごいパワーがあるんです。
理由1:品質が安定して、不良が減るんです!
「誰がやっても同じ品質」って、製造業の理想ですよね。マニュアルは、そのための「設計図」なんです。作業の手順や判断基準をきっちり決めておくことで、担当者によるバラつき(ムラ)をなくし、ミスを防ぐことができます。
例えば、ボルトの締め付けトルク、検査のチェック項目、材料の配合比率など、細かい部分まで標準化することで、「うっかりミス」や「勘違い」による不良品の発生をぐっと抑えられます。結果として、手直し(ムダ)も減って、コスト削減にも繋がるんです。
品質管理の基本は標準化であり、マニュアルはその土台となります。
不良品が減れば、それは直接的に利益の向上につながりますからね。
ポイント
マニュアルが単に問題が起きてから参照するものではなく、品質を作り込むための積極的な道具だということです。品質問題の多くは、手順のばらつきや基準の誤解から生まれます。 マニュアルは、これらの基準や手順を明確に定義します。全員がマニュアルに書かれた「正しい」手順に従うことを徹底すれば、不良につながる可能性のある作業のばらつきを、発生する前に最小限に抑えることができるのです。これは、品質管理の焦点を、後工程での検査や修正(受動的)から、工程内での予防(能動的)へと転換できる可能性を秘めています。
理由2:安全第一!ヒヤリハットも事故も防げる!
工場の安全は何よりも大切ですよね。マニュアルには、危険な作業の正しい手順や、守るべきルールを明確に記す役割があります。「この作業は保護メガネ必須!」「このスイッチは絶対に触らない!」といったルールを全員が確実に守ることで、ヒヤリハットや労災事故のリスクを大幅に減らせるんです。
機械の操作手順、化学薬品の取り扱い、高所作業の注意点など、危険が伴う作業ほど、写真や図解入りの分かりやすいマニュアルが効果を発揮します。「まあ、大丈夫だろう」という気の緩みが事故を招くこともあります。マニュアルで手順を再確認する習慣が、安全意識を高めるんですね。
安全教育の基本は、正しい手順の遵守を徹底することです。これは、5S活動(整理・整頓・清掃・清潔・しつけ)とも密接に関連しています。整理整頓された安全な環境を維持することも大切ですね。
ポイント
よく整備され、常に活用されるマニュアルは、単なる規則集ではありません。それは、安全に対する会社の姿勢を具体的に示すものとなり、日々の安全行動を強化します。安全は、確立された安全な作業手順を一貫して守ることで成り立ちます。マニュアルはこれらの手順を記録したものです。マニュアルが目に見える場所にあり、アクセスしやすく、特に普段行わない作業や危険な作業の際に定期的に参照されるようになれば、それは安全手順の絶え間ないリマインダーとして機能します。このような日常的なマニュアルとの関わりが、安全手順を日々のルーティンに組み込み、単なる規則遵守を超えて、マニュアルを確認すること自体が安全な操作方法であるという、深く根付いた安全文化へと繋がっていくのです。
理由3:新人教育も技術の引継ぎも、ぐっと楽になる!
「見て覚えろ!」のOJT(On-the-Job Training)だけでは、教える方も教わる方も大変ですよね。それに、教える人によって内容が違ったり、大事なコツが伝わらなかったり…。
「使えるマニュアル」があれば、基本的な手順はマニュアルで学んでもらい、OJTではより実践的な指導に集中できます。
例えば、動画マニュアルなら、ベテランの「匠の技」も分かりやすく記録して、技術継承に役立てられます。「あの人にしかできない」という属人化を防ぎ、誰かが休んでも業務が止まらない体制づくりにも繋がります。結果的に、教育にかかる時間やコストも削減できるんです。
属人化の解消、技術継承、教育効率化、そして多能工化(一人の作業者が複数の工程や作業を担当できるようになること)は、マニュアルがもたらす大きなメリットです。
ポイント
優れたマニュアルは、個人の専門知識(しばしば「暗黙知」として閉じ込められている)を、組織全体で共有・活用できる資産(「形式知」)へと転換します。これにより、知識を一貫して、かつ大規模に伝達することが可能になり、一対一の教育の限界を打ち破ることができるのです。製造業は特定のスキルやノウハウに大きく依存しています。その多くは、経験豊富な作業者の中に暗黙知として存在しています。従来のOJTは主要な伝達手段ですが、時間がかかり、一貫性がなく、教える側のスキルや時間に左右されます。これがボトルネックとなり、退職などによる知識喪失のリスク(属人化)を生みます。マニュアル、特に動画や画像を用いたものは、この暗黙知を捉え、明確な手順として文書化します。文書化された知識は、誰でも、いつでもアクセス可能な、再利用可能なスケーラブルなリソースとなります。これにより、基本的なトレーニングが熟練者の直接的な指導から切り離され、熟練者はより高度な指導や問題解決に集中できるようになり、組織全体で一貫した基礎知識の伝達が保証されるのです。
3. でも現実は…「うちのマニュアル、誰も見てない…」その原因とは?
ここまでマニュアルの重要性をお話ししてきましたが、「理想はそうだけど、うちでは全然活用されてないよ…」という声が聞こえてきそうです。そうなんです、残念ながら「使われないマニュアル」になってしまっているケースは、本当に多いんですよね。
では、なぜそうなってしまうのでしょうか? いくつか代表的な原因を見ていきましょう。
皆さんの工場にも当てはまるものがあるかもしれません。
原因1:「文字ばっかりで、読む気がしない…」
専門用語が多かったり、文章が長すぎたりすると、読むのが大変ですよね。特に現場で忙しく作業している時には、パッと見て理解できないと、もう読むのを諦めてしまいがちです。
原因2:「情報が古くて、今のやり方と違う…」
改善活動などで作業手順が変わったのに、マニュアルが更新されていないケース。これは非常に問題です。古い情報のままでは役に立たないどころか、間違った作業を助長してしまう危険性もあります。「どうせ古いでしょ?」と思われたら、もう見てもらえなくなりますね。
原因3:「どこにあるか分からない、探すのが面倒…」
マニュアルが必要な時に、すぐに見つけられない。保管場所が決まっていない、整理されていない、そもそも存在を知らされていない… これでは活用されませんよね。「探す時間」自体がムダになってしまいます。
原因4:「写真や図がなくて、イメージがわかない…」
特に製造現場の作業は、言葉だけでは伝わりにくいことが多いです。実際の機械の操作や、部品の向き、微妙な力加減などは、写真や図、動画がないと正確に理解するのが難しいですよね。
これらのマニュアルが活用されない原因(分かりにくい、古い、見つけにくい)は、実は単なる文書の問題ではなく、工場内の情報管理、コミュニケーション、そしてプロセスの規律といった、より根本的なシステムの問題を指し示していることが多いのです。
マニュアルが古くなるというのは手順が変更された際に文書を更新するプロセスが機能していない(改善活動と文書化が連携していない)、マニュアルが見つけにくいというのは情報の整理やアクセスの仕組みが不十分である、マニュアルが分かりにくく文字が多いというのは利用者中心の設計思考が欠けている、そして、効果的なビジュアル資料を作成するためのスキルやツールが不足している可能性を示唆します。現在の工場課題そのものです。
これらは文書自体の個別の欠陥ではなく、業務知識を管理し伝達するという、より広範な組織的弱点の現れなのです。マニュアルの問題を解決するには、単に文書を書き直すだけでなく、これらの根本的なプロセスを修正する必要があります。
4. 明日から実践!現場で本当に「使われる」マニュアル作成5つのコツ
では、どうすれば「使われるマニュアル」を作れるのでしょうか? 難しく考える必要はありません。
ちょっとしたコツを押さえるだけで、見違えるように分かりやすく、現場で役立つマニュアルが作れるんです。
ここでは5つのコツをご紹介します!
コツ1:見る人の気持ちになって、シンプルに!
マニュアルを作る時、つい専門用語を使ったり、詳しく書きすぎたりしがちですが、一番大切なのは「使う人が見てすぐわかるか?」です。新人さんや、他の部署の人でも理解できるよう、難しい言葉は避けて、一文を短く、簡潔に書くことを心がけましょう。
例えば、「〇〇装置のパラメータを△△に設定」ではなく、「〇〇装置の画面で、このボタンを押して、数字を△△に合わせてください」のように、具体的な操作をイメージできるように書くと良いですね。
コツ2:写真・図・動画でパッと見てわかる!
「百聞は一見にしかず」と言いますが、まさにその通り!
特に動きのある作業や、複雑な機械の操作は、写真やイラスト、短い動画を使うのが一番効果的です。
どこを見て、どう動かせばいいのか、一目でわかります。
工具の正しい持ち方、部品の向き、OK/NG事例などは、写真で見せるのが分かりやすいです。一連の作業の流れは、動画で見せると全体のイメージが掴みやすいですね。
Before-Afterの写真も改善効果が分かりやすくておすすめです。
コツ3:「なぜ?」と「注意点」をしっかり伝える!
ただ手順を並べるだけでなく、「なぜこの手順が必要なのか?」「これを守らないとどうなるのか?」という理由や背景、そして「特に注意すべき点」「やってはいけないこと」を明確に伝えることが重要です。
理由がわかれば、作業の意味を理解し、納得して取り組めますし、危険なポイントが分かっていれば、安全意識も高まります。
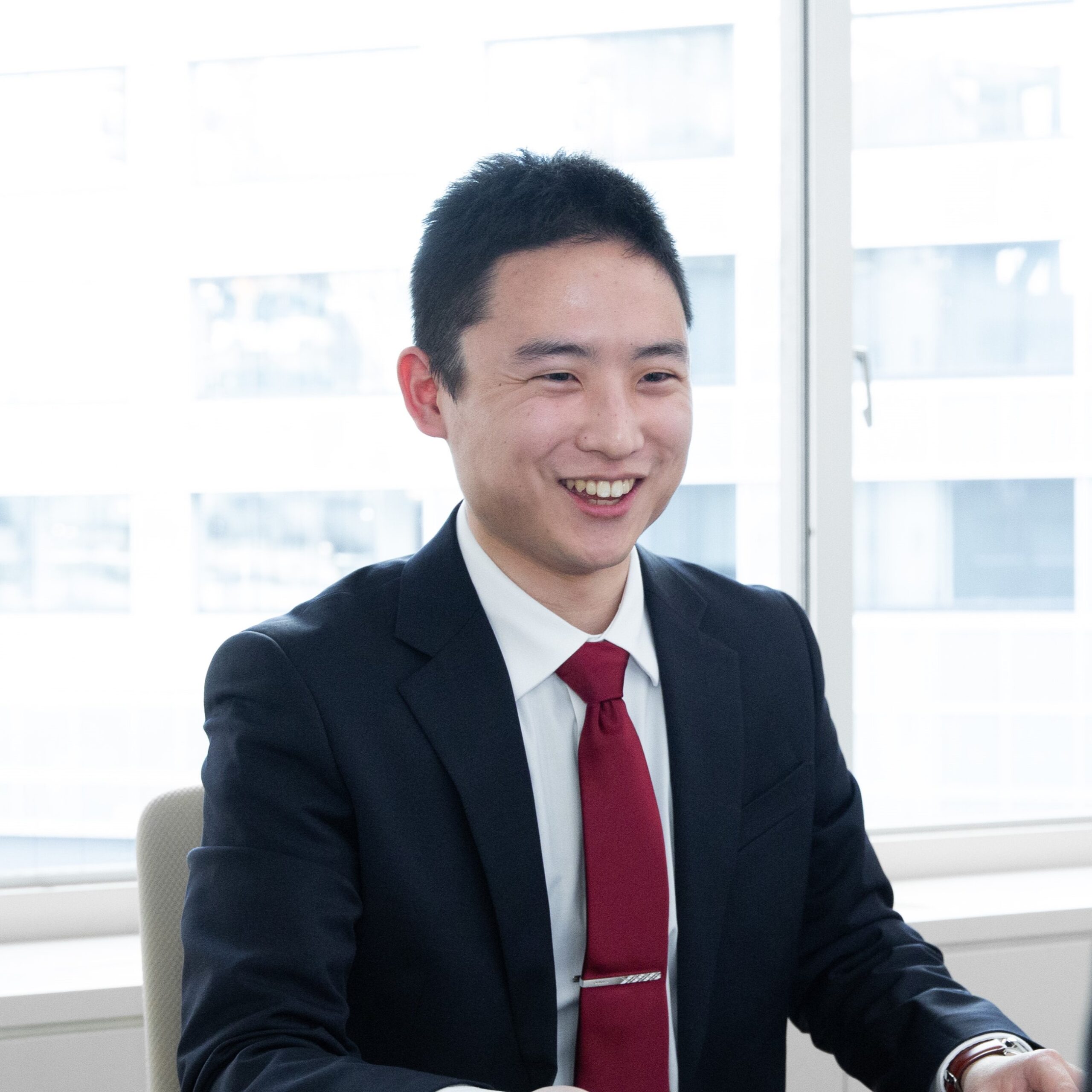
包丁の刃を触ってはいけないことは誰にでもわかりますが、なぜかというと、手が切れるからですよね。日頃その機械・装置を扱っていない人からしたら、手が切れてしまうことが分かりません。
例えば、「『清掃する』だけでなく、『清掃することで機械の異常を早期発見できます』と目的を書く。」「『このカバーは必ず閉めること(感電の危険あり!)』のように、危険箇所は赤字や太字、マークなどで目立たせましょう。」
コツ4:現場の知恵を借りる!
実際に作業している人が一番、分かりやすい手順や、気を付けるべきポイントを知っています。マニュアルを作る際は、必ず現場の作業者の方にヒアリングしたり、一緒に作ったりしましょう。ベテランの知恵や工夫(暗黙知)をマニュアルに盛り込むことで、より実践的で価値のあるものになります。
「この作業、いつもこうやると早くできるんだよ」というコツや、「ここはよく間違えやすいから気をつけて」という注意点を教えてもらい、マニュアルに反映させましょう。
コツ5:作った後も「育てる」意識で!
マニュアルは作って終わりではありません。業務内容が変わったり、もっと良い方法が見つかったりしたら、すぐに更新することが大切です。「マニュアルは常に最新の状態」を保つことで、信頼され、活用され続けるようになります。
定期的に見直し、改善していく「育てる」意識を持ちましょう。
更新担当者を決め、更新ルール(例:工程変更時は必ず更新、年1回定期見直し)を設けることが有効です。
更新したら、変更点を分かりやすく周知することも忘れずに。
これらのコツを実践することで、マニュアルは単なる静的な参考資料ではなく、日々の業務と改善活動(カイゼン)に積極的に組み込まれた、生きた文書になります。利用者中心の考え方、分かりやすさ、視覚情報、現場の知恵の活用は、マニュアルを日々の作業遂行に直接役立つものにします。そして、継続的な更新とプロセス変更との連動 は、作業が変わればマニュアルも更新され、更新されたマニュアルに従って作業が行われる、というフィードバックループを意味します。
さらに、作業者を巻き込み、「なぜ」を説明することで、当事者意識が育まれ、マニュアルを単なる規則遵守のためだけでなく、さらなる改善(カイゼン)の出発点として活用する文化が醸成されます。マニュアルが常に最善の方法を反映し、使いやすく更新されやすい状態にあれば、それは日々の業務遂行と継続的な改善サイクルの両方にとって不可欠な要素となり、単なる独立した静的な成果物ではなくなるのです。
5つのコツまとめ
よくある残念なマニュアル | こうすれば「使える」!改善のポイント | 期待できる効果 |
---|---|---|
文字だらけ / 専門用語が多い | シンプルな言葉、図・写真・動画を活用 | 理解度向上、作業時間短縮 |
情報が古い / 更新されない | 定期的な見直し・更新ルールを設定 | 正確な作業、信頼性向上 |
探しにくい / 保管場所不明 | 保管場所の明確化、デジタル化・ツール活用 | 検索時間削減、必要な時にすぐ活用 |
手順のみ / 理由・注意点がない | 「なぜ?」と注意点を明記、危険箇所は強調 | 作業意義の理解、安全意識向上 |
現場の声が反映されていない | 作成時に現場の作業者にヒアリング、一緒に作成 | 実践的な内容、納得感向上、改善意欲向上 |
5. とはいえ、マニュアル作りって結構大変ですよね…
ここまで「使えるマニュアル」のコツをお伝えしてきましたが、「言うは易し、行うは難し」ですよね…。
実際、分かりやすいマニュアルを一から作るのは、思った以上に時間も手間もかかるものです。
特に、現場の作業をしながら、写真や動画を撮って、文章を考えて、編集して…となると、担当者の負担はかなり大きくなってしまいます。
それに、ベテランの「感覚」や「コツ」といった言葉にしにくい部分(暗黙知)を、どうやって分かりやすく伝えるか、という難しさもありますね。
「マニュアルの重要性は分かっているけど、作る時間も人手も足りない…」「もっと効率よく、質の高いマニュアルを作りたい…」そんな風に感じている方も多いのではないでしょうか?
実は、マニュアル作成には専門的なノウハウが必要です。分かりやすい構成、伝わる文章、効果的な見せ方など、ポイントを押さえることで、格段に「使える」マニュアルになるんです。
ここで考えてみたいのは、不適切な内部作成による機会損失です。適切なスキルやツール、専任の時間がないまま社内でマニュアルを作成しようとすると、効果のないマニュアルができるだけでなく、本来、生産や改善活動に使うべき貴重なリソースを浪費してしまうという大きな機会損失が発生します。
良いマニュアルを作成するには、特定のスキル(文章力、デザイン、動画編集、教育設計など)と専任の時間が必要です。製造現場の担当者は、これらの専門スキルを持っていなかったり、本来の業務と並行してマニュアル作成に時間を割くことが難しかったりすることが多いです。彼らがマニュアル作成に時間を取られると、生産活動、監督業務、直接的な改善活動から離れることになります。さらに、もし社内で作成されたマニュアルが効果的でない(分かりにくい、古い、使われない)場合、作成に費やされた時間は本質的に無駄になり、かつ、マニュアルが解決すべきだった問題(品質のばらつき、安全リスク、教育の非効率)は解決されないまま残ります。つまり、効果のない内部作成には二重のコストがかかっているのです。費やされた時間の直接的なコストと、根本的な業務問題を解決できなかったことによる機会損失、そして他の価値ある業務からリソースを奪ったことによる機会損失です。この点を考慮すると、専門家による外部の支援は、トータルで見るとより費用対効果の高い解決策となり得るのです。
もし、自社だけで抱え込まずに、専門家の力を借りるという選択肢も考えてみてはいかがでしょうか?
6. RYOPONがお手伝いします!
現場で本当に役立つマニュアルは、品質安定、安全確保、そして人材育成の強力な武器になります。ですが、その作成には、現場を知る視点と、分かりやすく伝えるための専門的なノウハウが不可欠です。
「写真や動画をもっと活用したいけど、どうすれば効果的かわからない…」「更新作業が追いつかない…」「そもそも、どこから手をつければいいか…」そんなお悩みはありませんか?
私たちRYOPONは、製造現場に特化したマニュアル作成のプロフェッショナルです。皆さんの工場の状況をしっかりヒアリングし、現場で本当に「使える」、分かりやすいマニュアル作りを代行・サポートします。
写真や動画を効果的に活用したビジュアルマニュアルの作成、更新しやすい仕組みづくり、多言語対応もお任せください。
「うちの工場も、もっと良いマニュアルが欲しい!」そう思われたら、ぜひ一度RYOPONにご相談ください。初回のご相談は無料です。私たちが、皆さんの現場改善を力強くサポートします!まずはお気軽にお問い合わせくださいね。