業務改善で収益を向上する手法と事例
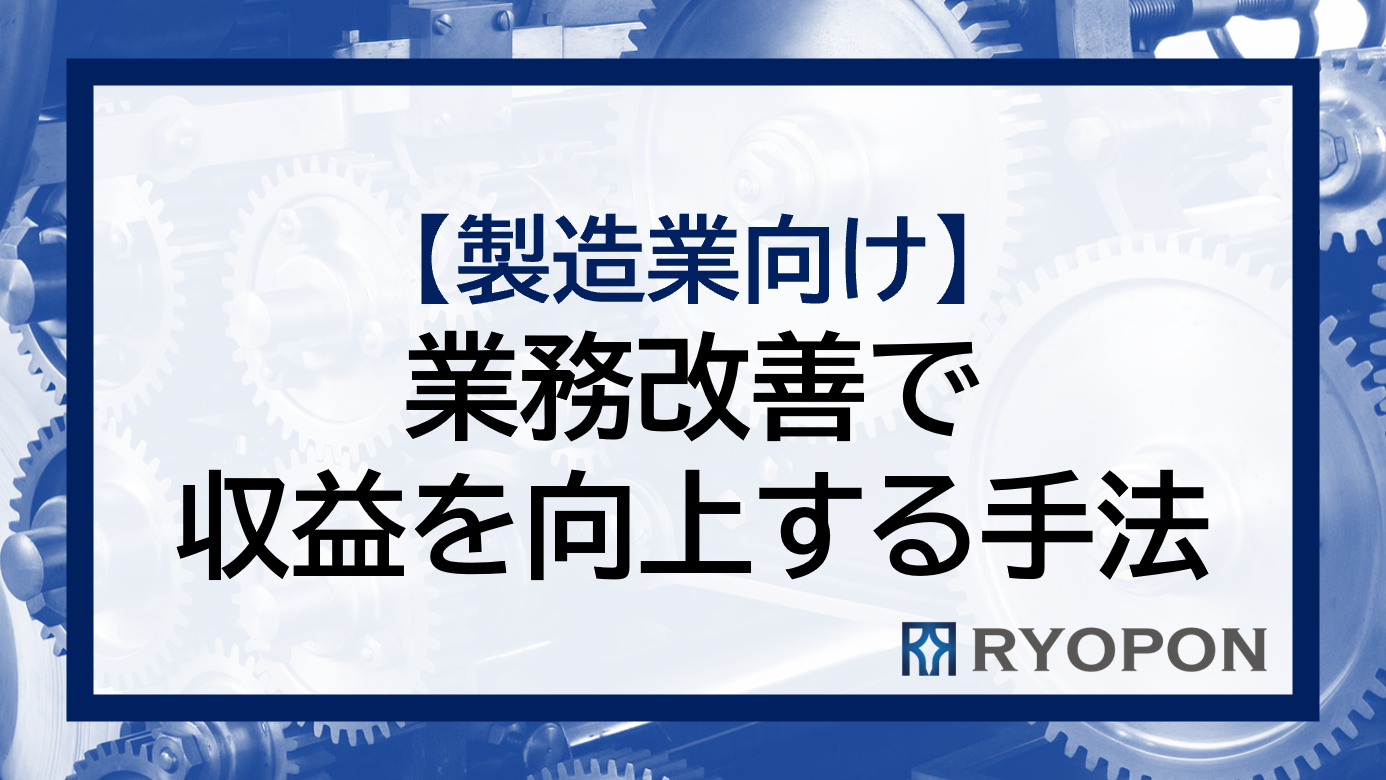
皆様、こんにちは。製造業収益改善パートナーの北澤です。 昨今、多くの中小製造業の皆様からご相談をいただく中で、収益改善の鍵として業務改善の重要性がますます高まっていると実感しております。業務の効率化は、生産性の向上やコスト削減に直結し、ひいては会社の競争力を底上げする力強いエンジンとなります。特に、製造の現場に潜むムダをなくし、働く皆様一人ひとりのスキルを最大限に引き出す取り組みが、今まさに求められています。
具体的な手法として、皆様も耳にしたことがあるかもしれませんが、「5S活動」や「カイゼン活動」が挙げられます。5S活動を徹底すれば、驚くほど職場環境が整い、探し物などの無駄な時間がなくなって作業効率が上がります。また、カイゼン活動では、現場で働く方々の声に真摯に耳を傾けることで、これまで見過ごされてきた問題点が浮かび上がり、素晴らしい改善案が生まれるのです。これらの地道な取り組みが、見えなかった問題を「見える化」し、解決へと導く確かな一歩となります。
さらに、忘れてはならないのがデータの活用です。生産データや工程データを丁寧に分析することで、勘や経験だけに頼らない、客観的な根拠に基づいた業務改善の方向性が見えてきます。これにより、真のムダを排除し、人や設備といった貴重なリソースを最適に配分することが可能になるのです。つまり、業務改善とは、単なる作業効率アップに留まらず、会社全体の収益構造そのものを変革する力を秘めているのです。
自社のどこから手をつければ良いか分からない、具体的な進め方が知りたい、という方もいらっしゃるでしょう。この記事が、皆様の第一歩を踏み出すきっかけとなれば幸いです。
業務改善とは何か
「業務改善」と聞くと、少し難しく聞こえるかもしれません。しかし、これは会社がより良く、より強く成長するために、効率と効果を最大限に高める一連の取り組みを指す言葉です。特に私たち中小製造業にとっては、限られたリソースの中でいかに生産性を高め、しっかりと収益を確保していくか、そのための生命線とも言えるプロセスです。業務改善は、単に作業の手順を見直すだけでなく、会社全体の文化や従業員の皆様のモチベーション向上にも深く関わる、非常に重要な活動なのです。
業務改善は、まず「現状を正しく知る」ことから始まります。生産プロセスや日々の業務の流れを一つひとつ丁寧に見ていき、どこに問題が潜んでいるのか、どこで流れが滞っているのか(ボトルネック)を特定します。その後、具体的な改善策を立てて実行することで、ムダをなくし、限りあるリソースを効率的に使うための道筋が見えてきます。この積み重ねが、生産性の向上やコスト削減に繋がり、結果として会社の収益を押し上げてくれるのです。
また、非常に重要なことですが、業務改善は一度やれば終わり、というものではありません。現場から得られた「やってみたらこうだった」という生のフィードバックを元に、常に改善策を見直し、評価し続けることが大切です。このように、業務改善は単なる効率化を超えた、会社の未来を創るための戦略的な活動であり、長期的な成功に大きく貢献してくれるのです。
業務改善の定義
業務改善をもう少し具体的に定義すると、それは企業において業務の効率性や効果を向上させるための、体系的なプロセスを指します。特に中小製造業の現場では、限られた資源を最大限に活かし、生産性を高めるための重要な手段として認識されています。多くの成功している企業では、業務改善を「PDCAサイクル」に基づいて進めています。つまり、計画(Plan)を立て、実行(Do)し、その結果をきちんと評価(Check)し、見つかった課題を次の計画に反映させる(Act)というサイクルを、粘り強く回し続けるのです。これにより、業務は継続的に磨かれていきます。
業務改善は、短期的なプロジェクトとして終わらせるのではなく、会社全体に根付く文化として育てていくことが何よりも重要です。現場の従業員の皆様からの「もっとこうしたら良くなるのでは?」という意見や提案こそが宝です。全員が参加する形で進めることで、改善は「やらされ仕事」ではなく、「自分たちの仕事を良くする活動」へと変わっていきます。そのための代表的な手法が、先ほども触れた「5S活動」や「カイゼン」であり、これらを通じて職場環境が整い、目に見える形で無駄が省かれていくのです。
業務改善は、会社が厳しい競争環境の中で勝ち残り、さらに成長していくための長期的な戦略でもあります。効率を追求するだけでなく、従業員の皆様が働きやすいと感じ、仕事へのやりがいを高めることにも繋がります。したがって、業務改善に真剣に取り組むことは、会社の未来に向けた、極めて重要な一歩となるのです。
POINT
- 現状把握からスタート: まずは自社の業務プロセスを正確に知ることが第一歩。
- 継続は力なり: 一度きりのイベントではなく、PDCAサイクルを回し続ける文化を築く。
- 全員参加が鍵: 経営層だけでなく、現場の従業員一人ひとりが主役となる。
業務改善の目的と必要性
では、なぜ私たちは業務改善に取り組む必要があるのでしょうか。その目的は、主に生産性の向上、コストの削減、品質の向上、そして何より顧客満足度の向上という、企業の成長に不可欠な4つの柱を太くすることにあります。私たち中小製造業において、限られたリソースを最大限に活かすことは、競争力を保つために絶対に欠かせない要素です。業務改善に取り組むことで、生産ラインの効率化や資源の適切な配置が実現し、これが直接的な収益アップへと繋がっていきます。
さらに、業務改善は良い企業文化を育むことにも直結します。従業員の皆様が改善活動に主体的に参加することで、仕事へのモチベーションが高まり、職場環境も活性化します。現場で働く人々の意見が尊重され、形になることで、「自分たちの力で会社を良くしている」という実感が生まれ、エンゲージメント、つまり仕事への熱意が高まります。その結果、チームワークが強固になり、社内のコミュニケーションも円滑になるなど、会社全体のパフォーマンス向上に繋がるのです。
また、業務改善は、変化の激しい現代の市場環境において、ますますその必要性が高まっています。経済のグローバル化や競争の激化の中で、中小製造業も常に変化を求められています。新しい技術の登場やお客様のニーズの多様化にしっかりと対応していくためには、柔軟かつ迅速に業務改善を行う俊敏性が重要になります。そうすることで、会社は変化をピンチではなくチャンスと捉え、生き残り、さらに成長していく道を切り拓くことができるのです。
何から始めれば良いのか、自社の課題はどこにあるのか、もしお悩みでしたら、ぜひ一度、私ども専門家にご相談ください。客観的な視点から、皆様の会社の状況に合わせた最適な改善プランをご提案いたします。
業務改善による収益向上の仕組み
業務改善がどのようにして収益アップに繋がるのか、その仕組みを分解してみましょう。ポイントは「コスト削減」「生産性向上」「品質向上」という3つの歯車が噛み合うことにあります。
コスト削減
まず、コスト削減です。これは業務改善を通じて収益を向上させるための、最も分かりやすく、かつ重要な鍵となります。業務に潜むあらゆる無駄を徹底的に排除することで、材料費や人件費、経費といった資源の投入を最小限に抑えることができます。これが直接的な利益の増加に繋がるのです。
例えば、在庫管理の見直しは非常に効果的です。必要なものを、必要な時に、必要なだけ持つ「ジャストインタイム」の考え方を取り入れることで、不要な在庫を抱えるための倉庫代や管理コストを大幅に削減し、会社のキャッシュフローを健全にすることができます。また、工場内の作業フローを見直し、作業者の移動距離を短くしたり、不要な工程そのものをなくしたりすることも、生産コストの低減に大きく貢献します。
人件費の最適化も重要です。これは単に人を減らすということではありません。業務の標準化やマニュアル整備を進め、作業ミスを減らすこと。あるいは、従業員への教育を通じて多能工化を進め、一人が複数の工程を担えるようにすること。これらは結果的に、残業時間の削減などに繋がり、人件費を抑制します。さらに、長期的な視点でサプライヤー様と良好な関係を築き、価格や納期の交渉を行うことも、原材料費の削減に繋がる重要な活動です。
生産性の向上
次に、生産性の向上です。業務改善によって作業フローがスムーズになり、無駄な待ち時間や手戻りが削減されると、従業員の皆様はより効果的に作業を進められるようになります。同じ時間内により多くの価値を生み出せるようになること、これが生産性向上の本質です。生産量が増えれば、それは直接売上の増加に貢献します。
生産性を上げるためには、まず作業フローの徹底的な見直しが必要です。各工程の無駄を洗い出し、プロセスを最適化することで、従業員がストレスなく、スムーズに働ける環境を整えます。作業手順を標準化し、誰がやっても同じ品質・同じ時間で作業できる体制を築くことは、品質の安定と効率化の両面に効果があります。適切な機械や治具を導入することも、もちろん生産性向上に大きく寄実に寄与します。
POINT
- コスト削減: 在庫、工程、人件費など、あらゆるムダを徹底的に排除する。
- 生産性向上: 同じ時間とリソースで、より多くの価値(製品)を生み出す。
- 品質向上: 顧客の信頼を獲得し、リピートや新規顧客に繋げる。
従業員のスキルアップ
業務改善を本当の意味で成功に導くためには、従業員一人ひとりのスキルアップが絶対に欠かせません。従業員の皆様が持つ技能や知識が高まることで、業務プロセス全体が円滑に流れ始め、結果として会社全体の生産性が向上するのです。
スキルアップは、従業員の皆様が自分の仕事に自信と誇りを持って取り組むための土台となります。そのために、会社は定期的な研修やワークショップの機会を提供することが効果的です。例えば、新しい機械の操作研修や、品質管理に関する勉強会を行うことで、従業員はより迅速かつ効率的に、そして質の高い仕事ができるようになります。これは、製造現場でのミスを減らし、製品の品質向上にも直接的に貢献します。
高品質な製品は、お客様からの信頼を獲得し、リピート購入や口コミによる新規顧客の獲得に繋がります。このように、業務改善から始まる品質向上は、会社の収益に大きなインパクトを与えるのです。
また、スキルアップは個人の成長に留まりません。従業員同士が知識を共有し、助け合う文化が育まれることで、チーム全体のパフォーマンスが向上します。問題解決能力の高い、強い組織が生まれるのです。
最後に、従業員の成長を積極的に支援する姿勢は、会社が人材を大切にしているという何よりのメッセージになります。従業員の皆様は会社への信頼を深め、これが定着率の向上や、優秀な人材の確保にも繋がっていくのです。従業員のスキルアップは、会社と従業員の双方にとってWIN-WINの関係を築くための、最も重要な投資と言えるでしょう。
業務改善のステップ
さて、ここからは業務改善を成功に導くための具体的なステップについてお話しします。闇雲に進めるのではなく、しっかりとした手順を踏むことが成功の鍵です。
現状分析と課題の可視化
業務改善のすべての始まりは、「現状分析と課題の可視化」です。この最初のステップがしっかりと行われるかどうかで、その後の改善活動の成果が大きく変わってきます。まずは、現場で起きていることを正確に把握するためのデータ収集が不可欠です。生産ラインの各工程にかかる時間(サイクルタイム)、機械の稼働率、材料のロス率など、具体的な数値を集めて分析します。
次に、データと同じくらい重要なのが、従業員からのヒアリングです。現場で毎日働いている従業員の皆様は、日々の業務の中で感じている問題点や「やりにくさ」を最もよく知っています。彼らの声に真摯に耳を傾け、現場の実態を反映させることで、課題をより正確に、そして深く捉えることができます。
集めたデータや意見をもとに、問題点を「見える化」していきます。どの工程で時間がかかっているのか、どの作業でミスが多いのか、といった具体的な課題を、グラフやフローチャートなどを使って誰もが一目で分かる形にまとめます。
この「現状分析と課題の可視化」は、業務改善という航海の海図を作るようなものです。どこに浅瀬や岩礁(問題点)があるのかを正確に把握することで、初めて安全で確実な航路(改善計画)を描くことができるのです。
目標設定と計画立案
現状分析を通じて課題が明らかになったら、ステップ2は「目標設定と計画立案」です。次の段階では、その課題を解決した先に、どのような状態を目指すのか、明確なゴールを設定します。この目標は、「頑張る」といった曖昧なものではなく、「誰が見ても達成できたかどうかが分かる」具体的な数値で示すべきです。例えば、「〇〇ラインの生産性を10%向上させる」「不良品率を現状の5%から2%に削減する」といった形です。
目標が定まったら、それを達成するための具体的な計画を立てます。この計画には、「誰が」「何を」「いつまでに」行うのかを明確に盛り込むことが不可欠です。責任者を定め、それぞれの役割分担をはっきりさせることで、計画は絵に描いた餅で終わらず、着実に実行へと移されます。
さらに、計画には進捗を測るためのマイルストーン(中間目標)を設定しておくと、よりスムーズに進みます。定期的にチームで進捗状況を確認し合うことで、問題が起きても早期に発見し、迅速に対応することが可能になります。このように、しっかりとした目標設定と緻密な計画立案こそが、業務改善を成功へと導く羅針盤となるのです。
実行とモニタリング
計画ができあがれば、いよいよステップ3、「実行とモニタリング」のフェーズです。これは、立てた計画を現場で実際に動かし、その成果を継続的に見守っていく、改善活動の心臓部とも言える段階です。
まず「実行」にあたっては、関係者全員が計画の目的と自分の役割を正しく理解し、一枚岩となって協力し合うことが不可欠です。特に、従業員の皆様の意識が成果を大きく左右するため、改善活動の目的や狙いを丁寧に説明し、共感を得ることが重要になります。現場での実行を後押しするために、必要なツールや資源を会社がしっかりと準備し、必要であれば研修なども実施することが効果的です。
次に「モニタリング」です。これは、実行した改善策が狙い通りの成果を生んでいるか、データや指標を用いて客観的に確認していく活動です。定期的にリーダーやチームメンバーが集まり、進捗状況をチェックする場を設けましょう。もし計画通りに進んでいなかったり、新たな問題が発生したりした場合には、迅速に対応できる体制を築いておくことが重要です。実際のデータに基づいて評価を行うことで、改善策の有効性が明確になり、さらなる改善へと繋げることができます。
この「実行とモニタリング」は、業務改善を成功させるために絶対に欠かせません。常に結果を把握し、柔軟に対応し続けることで、改善活動は一過性のものでなく、持続可能な会社の力へと発展していくのです。
効果の検証と最適化
業務改善の最後のステップは、「効果の検証と最適化」です。この段階では、実行した改善策がどれほどの効果を上げたのかを客観的に評価し、その結果に基づいて、さらなる高みを目指すための調整を行います。
まず何よりも、改善前と改善後のデータを比較分析することが重要です。生産性は上がったのか、コストは下がったのか、納期は短縮できたのか。事前に設定した目標に対して、どれくらい達成できたのかを数値で明確に評価します。この検証によって、改善策の本当の効果が明らかになり、次のアクションを決めるための確かな土台ができます。
期待通りの効果が確認できた場合、その改善策を標準化し、定着させるプロセスが大切になります。成功したやり方をマニュアルに落とし込んだり、他の部署にも展開したりすることで、その効果を会社全体で持続的に享受できるようになります。
一方で、目標が達成できなかったり、新たな問題が見つかったりした場合には、その原因を徹底的に突き止め、適切な修正を行います。決して失敗と捉えるのではなく、現場からのフィードバックを真摯に受け止め、プロセスを見直したり、別のアプローチを試したりすることで、改善のサイクルは止まることなく回り続けます。
このように、「効果の検証と最適化」のステップを定期的に繰り返すことで、業務改善は常に進化し続け、より高いレベルでの収益向上を実現することができるのです。
具体的な計画立案や効果検証の方法でお困りの際は、私たち専門家が皆様の状況に合わせたサポートをいたします。お気軽にお声がけください。
業務改善に役立つフレームワーク
業務改善には、先人たちの知恵が詰まった便利な「型」、つまりフレームワークが存在します。これらを活用することで、闇雲に考えるのではなく、思考が整理され、迷うことなく改善活動を進めることができます。ここでは、代表的なフレームワークをいくつかご紹介します。
PDCAサイクル
まず、業務改善の王道とも言えるのが「PDCAサイクル」です。これは、「Plan(計画)→ Do(実行)→ Check(評価)→ Act(改善)」という4つのステップを繰り返し回していくことで、業務を継続的にレベルアップさせていく手法です。特に私たち製造業においては、生産プロセスの見直しや効率化に向けて、このサイクルを地道に回し続けることが非常に重要です。具体的な目標を立て、その結果を数字で確認しながら改善を進めることで、螺旋階段を上るように着実に成果を積み上げていくことができます。
ECRS(イクルス)
ECRS(イクルス)も、現場ですぐに使える強力なフレームワークです。これは、「Eliminate(排除)」「Combine(結合)」「Rearrange(再配置)」「Simplify(簡素化)」という4つの改善の視点を表した言葉です。
- Eliminate(排除): 「この作業、本当になくせないか?」と問いかけ、不要な工程や作業そのものをなくします。
- Combine(結合): 別々の工程や作業を「一つにまとめられないか?」と考え、効率化を図ります。
- Rearrange(再配置): 作業の順番や場所を「入れ替えたらもっと良くならないか?」と見直し、流れをスムーズにします。
- Simplify(簡素化): 「もっと単純に、簡単にできないか?」と考え、作業の負担を軽減します。
この4つの視点で今の業務を見直すだけで、多くの改善のヒントが見つかるはずです。
バリューチェーン分析
バリューチェーン分析は、自社の事業活動を一つの「価値の連鎖」として捉え、どの工程で価値(バリュー)が生み出されているのかを分析する手法です。原材料の調達から製造、出荷、販売、アフターサービスに至る一連の流れ(主活動)と、それらを支える技術開発や人事管理など(支援活動)に分解し、自社の強みと弱みを明らかにします。これにより、どの部分に改善のメスを入れれば、最も効果的に競争力を高められるのかを戦略的に判断することができます。
これらのフレームワークは、業務改善を進める上での心強い武器となります。一つひとつを完璧に使いこなす必要はありません。自社の状況に合わせて、使えそうなものから試してみてはいかがでしょうか。
成功につながった具体例の紹介
理論だけでなく、実際に業務改善で大きな成果を上げられた企業の事例をご紹介しましょう。皆様の会社でも応用できるヒントがきっと見つかるはずです。
事例1: 5Sとカイゼン活動でコスト15%削減(製造業A社)
A社では、製品の生産過程で発生する材料のロスや、工具を探す時間といった無駄が大きな問題となっていました。そこで、全社を挙げて「5S活動(整理・整頓・清掃・清潔・躾)」を徹底し、職場環境の整備に着手しました。職人の皆様が自ら意見を出し合い、最も使いやすい工具の配置や部品の置き場を決めていきました。その結果、探し物の時間が劇的に減るなど、作業効率が大幅に向上。さらに、継続的な「カイゼン活動」を通じて、生産コストを15%も削減し、収益を大きく伸ばすことに成功しました。
事例2: AI-OCR×RPA導入で事務作業時間を70%削減!(製造業C社)
C社では、紙の注文書や請求書の処理に多くの人手と時間がかかっており、入力ミスも頻発していました。この課題を解決するため、同社はAI-OCR(手書き文字も読み取れるAI技術)とRPA(PC作業の自動化ツール)の導入を決断しました。まずAI-OCRで書類を自動でデータ化し、そのデータをRPAが基幹システムへ自動入力する仕組みを構築したのです。この結果、毎月のデータ入力にかかる作業時間を約70%も削減することに成功。人的ミスもほぼなくなり、従業員の皆様は、より付加価値の高い創造的な仕事に時間を使えるようになりました。
事例3: 既存システムの最適化でコスト20%ダウン!(製造業D社)
D社は、長年使い続けてきた古い生産管理システムが足かせとなり、データの集計や処理に膨大な時間がかかっていました。そこで、思い切って既存システムの最適化に着手。社内チームが中心となって業務フローを徹底的に見直し、本当に必要な機能は何かを洗い出しました。その上で、リアルタイムで生産状況を把握できる、新しいプラットフォームへと移行したのです。これにより、これまで手作業で行っていた集計業務などが自動化され、作業時間が大幅に短縮。迅速な意思決定も可能になり、結果として約20%ものコストダウンを実現しました。
これらの事例は、地道な現場改善から最新技術の活用まで、アプローチは様々ですが、いずれも「現状を正しく把握し、勇気を持って変革に踏み出した」という共通点があります。皆様の会社にも、必ず改善のヒントが眠っているはずです。
まとめ
ここまでお読みいただき、ありがとうございます。 業務改善は、私たち中小製造業の未来を切り拓くための、非常に強力な羅針盤となります。5S活動やカイゼン活動といった現場での地道な取り組みから、データ分析や最新技術の活用に至るまで、その手法は多岐にわたります。しかし、その根底にあるのは、「現状をより良くしたい」という強い想いです。
重要なのは、業務改善を一過性のイベントで終わらせるのではなく、従業員一人ひとりが改善意識を当たり前に持つような、強い組織文化を育んでいくことです。経営者や管理職の皆様には、ぜひその旗振り役となっていただきたいと思います。
業務改善の道のりは、決して平坦ではないかもしれません。しかし、その先には、生産性や品質が向上し、コストが削減され、従業員の皆様が生き生きと働き、そして何より、会社の収益が力強く伸びていく未来が待っています。
「何から始めたらいいか分からない」 「自社だけで進めるのは不安だ」
もしそう感じていらっしゃるなら、どうか一人で抱え込まないでください。私たち専門家は、皆様の会社に眠る可能性を最大限に引き出すためのパートナーです。最初の一歩を、私たちと一緒に踏み出しませんか?
貴社の現場は、もっと良くなる。
その可能性を、私たちと一緒に見つけませんか?
まずはお気軽にご相談ください。
貴社の課題解決への第一歩をサポートします。
製造現場を知り尽くしたパートナーとして、貴社の成長を全力で支援します。
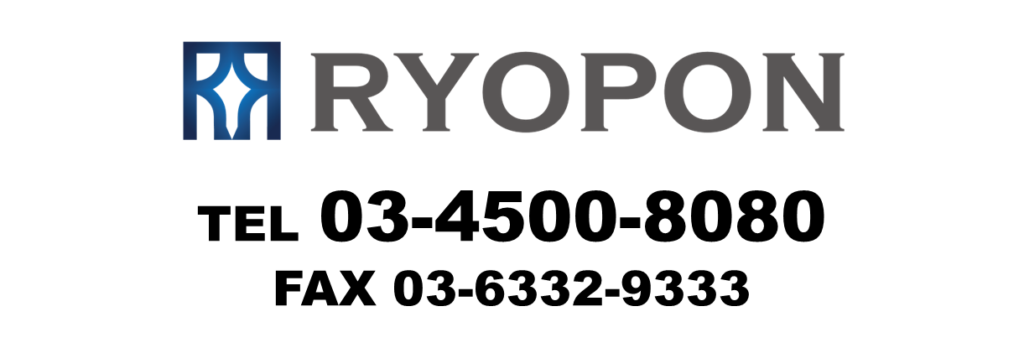